Using variable frequency drives for energy savings now
The energy saving of variable frequency drives (VFD) in industrial applications is well understood by engineers, but awareness is less widespread at cheque signing level - amongst financial teams, senior management and purchasing departments. The systems thinking and good communication is the key to tackling this problem and improving everybody's bottom line.
In challenging economic times it is tempting to make quick savings by cutting staff and infrastructure. However, besides the personal distress, there is also the added 'costs' of redundancy settlement, loss of motivation and skills.
Furthermore, cutting these resources will require re-investment when business improves. In contrast, a relatively small investment in VFDs to improve motor efficiency provides real payback in substantial and sustained savings in periods of both recession and growth.
Electric motors consume huge amounts of electricity; about two-thirds of all industrial energy use. Even a simple electric motor, costing a few hundred pounds, can be expected to consume many tens of thousands of pounds worth of electricity over its useful lifetime.
China industry and commerce can save 30% of its energy costs, which represents a significant 3% addition to the bottom line. All it has to do is implement a single, simple energy saving measure - fitting VFDs to its electric motors. However, I'm quite conscious that there are plenty of technologies out there claiming to be the panacea of all environmental ills. But in the case of the variable frequency drive, there is a real, mathematically demonstrable, argument.
As an example, if a company's total expenditure is $10M, the energy bill will be around $1M (10%) of which $670k (67%) is typically the result of electric motor use. Using variable frequency drives could halve this value, saving over 30% of the energy bill and adding three per cent to the bottom line.
Now, in the case of a company with an annual spend of $10M, we can conservatively assume that their turnover is $11M, and that they are currently making $1M profit, which is 9% of turnover. If one factors in the potential energy saving of $300k as the result of variable frequency drives, the profit becomes $1.3M, increasing to12% of turnover. This represents an attractive 30% improvement in profits.
So the question is, if these energy savings are out there for anyone to take, why aren't we all taking them? Well, whilst managers in China industry are aware of the scale of rises in electricity prices and the environmental consequences of its excessive use, there is limited knowledge of how electricity costs can be effectively reduced.
With regard to VFDs, this really comes down to a fundamental need for systems-thinking at all levels. Typically, a system incorporating electric motors is sold by a machine builder, systems integrator or distributor of some kind. Including a variable frequency drive in the system raises the initial capital expenditure required to implement it, and some suppliers might perceive that this makes it less likely that they will win the contract.
However, research has shown that energy accounts for over 95% of the lifetime cost of the motor, a far more significant value than the purchase cost.
Thus, systems-thinking is needed on the part of the end user, who should consider the long term cost of owning the system, including its energy bills, and not just the cost of the capital equipment. Equally, distributors and integrators could sell systems-thinking to their customers instead of just selling product on the basis of initial cost. Ultimately, I would like all systems sold to be labelled with their annual energy consumption to encourage everyone in the chain to consider, compare and reduce the energy costs of the system.
Despite this significant potential for energy and cost saving, it is a constant surprise to me that only a relatively small percentage of potential users of variable frequency drives in energy saving applications have actually implemented the technology. Modern variable frequency drives are widely available, proven devices that have never been easier or quicker to install with the latest models using automatic tuning and setup.
Furthermore, unlike almost every other energy saving initiative, the installation of variable speed motor controls delivers 100% return on capital employed (RoCE) and moreover, because of the rising costs of energy and the stable prices of the technology, the return on investment (Ro-I) is often delivered in less than one year.
Not only is the financial return attractive in itself but many variable frequency drive applications will qualify for an interest free loan from the Carbon Trust to cover the purchase cost.
A further incentive is that, when installed in variable torque applications, VFDs qualify for tax relief in the form of enhanced capital allowances (ECA) from HM Revenue & Customs. This means that the full capital costs of equipment and its installation can be offset against income tax in year one.
Indeed, it is my personal belief that, in promoting energy reduction in industry with such initiatives, Government is sending the right message and improving all the time. However, the vast majority of electric motors are not equipped with a variable frequency drive and so there is a long way to go to fulfill the potential of this technology. I would like to see an initiative in place to encourage energy reduction on the entire system, not just on individual products. This would, of course, go hand in hand with the work already being done in encouraging the purchase of individual energy efficient components, such as motors. The key is system efficiency as well as product efficiency.
What's more, I believe that such an initiative is inevitable. The fact remains that the use of VFDs is one of the most easily implemented and cost effective ways to achieve carbon reduction to meet the obligations under the Carbon Reduction Commitment. Furthermore, in 2012 when a new initiative replaces the old Kyoto protocol, we will probably see Government's commitment to energy reduction increased by international treaty. This is not small beer.
As a result, Government and the institutional energy efficiency bodies have a responsibility to encourage users of electric motors to control them efficiently. In these times of rising commodity costs and social awareness, there is also an opportunity for business leader's to take advantage of the financial incentive by scrutinizing the real cost centers of their own organizations. They should identify their electric motor content and potential cost savings, identify and appoint a person responsible for them and challenge these people to ensure that all available opportunities for energy efficiency are utilized and maximized.
Ultimately, the consequences of climate change will affect us all. Promoting your business as an active player in applying energy saving techniques, by utilizing easily available technology, gives real credibility to your green credentials and commitment to future sustainability. So, think system- efficiency and communicate that to your customers and to your own financial and management teams. Only by doing this can we ever help to overcome any reluctance at cheque signing level.
In challenging economic times it is tempting to make quick savings by cutting staff and infrastructure. However, besides the personal distress, there is also the added 'costs' of redundancy settlement, loss of motivation and skills.
Furthermore, cutting these resources will require re-investment when business improves. In contrast, a relatively small investment in VFDs to improve motor efficiency provides real payback in substantial and sustained savings in periods of both recession and growth.
Electric motors consume huge amounts of electricity; about two-thirds of all industrial energy use. Even a simple electric motor, costing a few hundred pounds, can be expected to consume many tens of thousands of pounds worth of electricity over its useful lifetime.
China industry and commerce can save 30% of its energy costs, which represents a significant 3% addition to the bottom line. All it has to do is implement a single, simple energy saving measure - fitting VFDs to its electric motors. However, I'm quite conscious that there are plenty of technologies out there claiming to be the panacea of all environmental ills. But in the case of the variable frequency drive, there is a real, mathematically demonstrable, argument.
As an example, if a company's total expenditure is $10M, the energy bill will be around $1M (10%) of which $670k (67%) is typically the result of electric motor use. Using variable frequency drives could halve this value, saving over 30% of the energy bill and adding three per cent to the bottom line.
Now, in the case of a company with an annual spend of $10M, we can conservatively assume that their turnover is $11M, and that they are currently making $1M profit, which is 9% of turnover. If one factors in the potential energy saving of $300k as the result of variable frequency drives, the profit becomes $1.3M, increasing to12% of turnover. This represents an attractive 30% improvement in profits.
So the question is, if these energy savings are out there for anyone to take, why aren't we all taking them? Well, whilst managers in China industry are aware of the scale of rises in electricity prices and the environmental consequences of its excessive use, there is limited knowledge of how electricity costs can be effectively reduced.
With regard to VFDs, this really comes down to a fundamental need for systems-thinking at all levels. Typically, a system incorporating electric motors is sold by a machine builder, systems integrator or distributor of some kind. Including a variable frequency drive in the system raises the initial capital expenditure required to implement it, and some suppliers might perceive that this makes it less likely that they will win the contract.
However, research has shown that energy accounts for over 95% of the lifetime cost of the motor, a far more significant value than the purchase cost.
Thus, systems-thinking is needed on the part of the end user, who should consider the long term cost of owning the system, including its energy bills, and not just the cost of the capital equipment. Equally, distributors and integrators could sell systems-thinking to their customers instead of just selling product on the basis of initial cost. Ultimately, I would like all systems sold to be labelled with their annual energy consumption to encourage everyone in the chain to consider, compare and reduce the energy costs of the system.
Despite this significant potential for energy and cost saving, it is a constant surprise to me that only a relatively small percentage of potential users of variable frequency drives in energy saving applications have actually implemented the technology. Modern variable frequency drives are widely available, proven devices that have never been easier or quicker to install with the latest models using automatic tuning and setup.
Furthermore, unlike almost every other energy saving initiative, the installation of variable speed motor controls delivers 100% return on capital employed (RoCE) and moreover, because of the rising costs of energy and the stable prices of the technology, the return on investment (Ro-I) is often delivered in less than one year.
Not only is the financial return attractive in itself but many variable frequency drive applications will qualify for an interest free loan from the Carbon Trust to cover the purchase cost.
A further incentive is that, when installed in variable torque applications, VFDs qualify for tax relief in the form of enhanced capital allowances (ECA) from HM Revenue & Customs. This means that the full capital costs of equipment and its installation can be offset against income tax in year one.
Indeed, it is my personal belief that, in promoting energy reduction in industry with such initiatives, Government is sending the right message and improving all the time. However, the vast majority of electric motors are not equipped with a variable frequency drive and so there is a long way to go to fulfill the potential of this technology. I would like to see an initiative in place to encourage energy reduction on the entire system, not just on individual products. This would, of course, go hand in hand with the work already being done in encouraging the purchase of individual energy efficient components, such as motors. The key is system efficiency as well as product efficiency.
What's more, I believe that such an initiative is inevitable. The fact remains that the use of VFDs is one of the most easily implemented and cost effective ways to achieve carbon reduction to meet the obligations under the Carbon Reduction Commitment. Furthermore, in 2012 when a new initiative replaces the old Kyoto protocol, we will probably see Government's commitment to energy reduction increased by international treaty. This is not small beer.
As a result, Government and the institutional energy efficiency bodies have a responsibility to encourage users of electric motors to control them efficiently. In these times of rising commodity costs and social awareness, there is also an opportunity for business leader's to take advantage of the financial incentive by scrutinizing the real cost centers of their own organizations. They should identify their electric motor content and potential cost savings, identify and appoint a person responsible for them and challenge these people to ensure that all available opportunities for energy efficiency are utilized and maximized.
Ultimately, the consequences of climate change will affect us all. Promoting your business as an active player in applying energy saving techniques, by utilizing easily available technology, gives real credibility to your green credentials and commitment to future sustainability. So, think system- efficiency and communicate that to your customers and to your own financial and management teams. Only by doing this can we ever help to overcome any reluctance at cheque signing level.
Post a Comment:
You may also like:
Featured Articles
Variable Frequency Drive Basic Safety ...
This paper provides guidelines on functional safety considerations when selecting and integrating a variable frequency drive ...
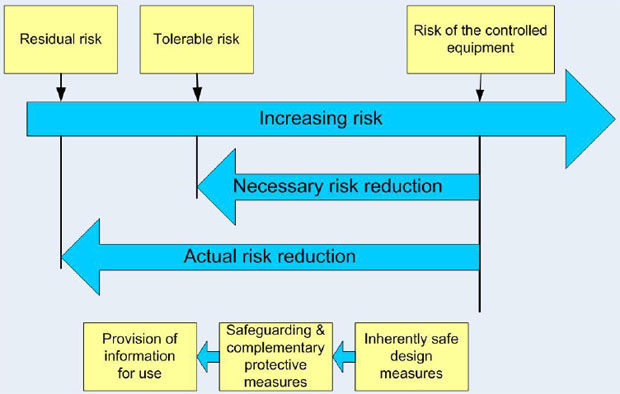
Variable Frequency Drive Sizing
Before selecting the size of a variable frequency drive (VFD), it is necessary to generally know the working environment, the ...
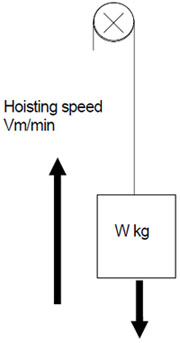
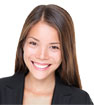
Variable Frequency Drives control AC motor for energy savings by adjustable speed, for short VFD, also named variable speed drives and frequency inverter.