Home » Applications
Compensatory externals to aid in starting torque generation for synchronous motors are also basically expense burdens that need not be borne.
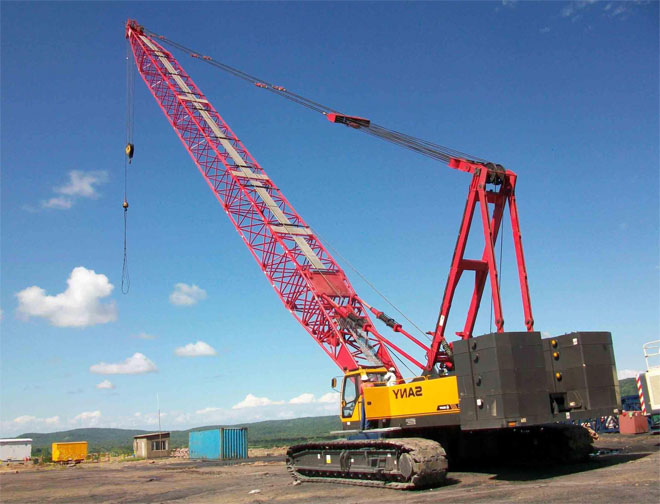
The cost of the synchronous motor itself over the asynchronous motor, with increased in frame size, added copper and other materials, is another base reason synch motors are seldom, if ever used in the overhead hoist and crane industry. As far as precise travel and lifting speeds with cranes, variable frequency drives with the hardware and software fairly standard on most variable frequency drives (VFD) designed for the application, is more than adequate. These variable frequency drives not only deliver excellent efficacy and significant energy savings by maintaining very good Volts/Hz/RPM ratios. Utilizing motor speed regulation at 0.5% without an encoder and 0.1% with asynchronous motors, makes the most opted for joint overhead crane control package.
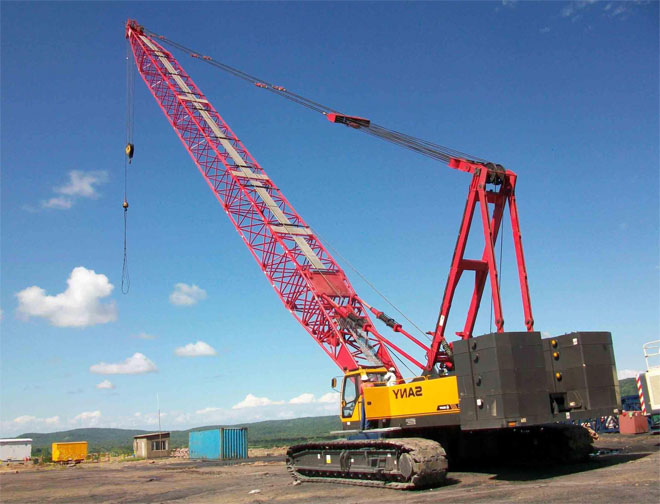
The cost of the synchronous motor itself over the asynchronous motor, with increased in frame size, added copper and other materials, is another base reason synch motors are seldom, if ever used in the overhead hoist and crane industry. As far as precise travel and lifting speeds with cranes, variable frequency drives with the hardware and software fairly standard on most variable frequency drives (VFD) designed for the application, is more than adequate. These variable frequency drives not only deliver excellent efficacy and significant energy savings by maintaining very good Volts/Hz/RPM ratios. Utilizing motor speed regulation at 0.5% without an encoder and 0.1% with asynchronous motors, makes the most opted for joint overhead crane control package.
Variable frequency drives convert incoming alternating current (AC) to direct current (DC) and then invert the DC power into variable frequencies and voltage AC power. Most variable frequency drives produce a constant voltage/frequency (hz)ratio.
One of the most common methods of varying pump shaft speed is to use a VFD. These VFDs take advantage of the fact that torque, speed and horsepower of an AC electric motor are related to the frequency and voltage of the electrical power supply.
For the VFD to be a sensible solution to your pumping application the system curve would have to fall on, or close to this best efficiency point line, or you will experience radial loads that will translate to shaft deflection. Most centrifugal pump companies want you to operate within 5% to 10% of the best efficiency point. Heavy duty pumps that have a low L3/D4 (shaft diameter to shaft length ratio) have a much larger operating window.
One of the most common methods of varying pump shaft speed is to use a VFD. These VFDs take advantage of the fact that torque, speed and horsepower of an AC electric motor are related to the frequency and voltage of the electrical power supply.
For the VFD to be a sensible solution to your pumping application the system curve would have to fall on, or close to this best efficiency point line, or you will experience radial loads that will translate to shaft deflection. Most centrifugal pump companies want you to operate within 5% to 10% of the best efficiency point. Heavy duty pumps that have a low L3/D4 (shaft diameter to shaft length ratio) have a much larger operating window.
Applying a variable frequency drive (VFD) to the heating system (see Figure 2) and a temperature sensor, the hot water temperature to the building zones can be better maintained by varying the flow of water.
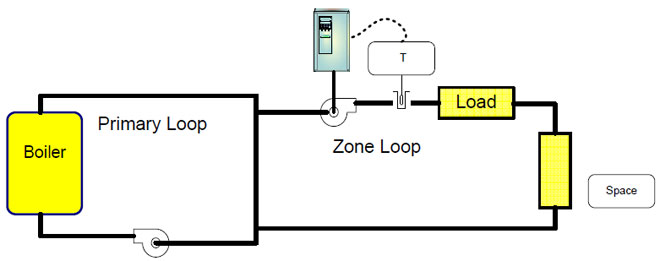
Energy Savings result from reduced electrical costs by reducing the speed of the pump and by better temperature control - preventing temperature over-shoot (over heating) in the zones. In many applications the pumps are oversized (10 to 15%), so even in maximum heat load conditions, the maximum pump speed with the variable frequency drive is less than before the retrofit.
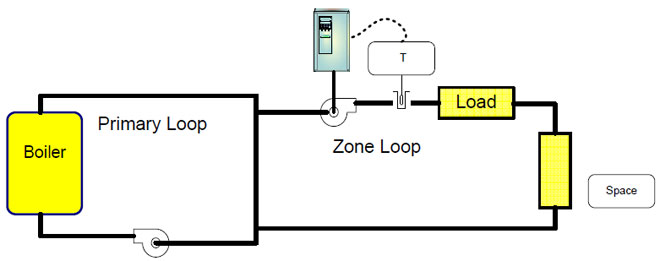
Energy Savings result from reduced electrical costs by reducing the speed of the pump and by better temperature control - preventing temperature over-shoot (over heating) in the zones. In many applications the pumps are oversized (10 to 15%), so even in maximum heat load conditions, the maximum pump speed with the variable frequency drive is less than before the retrofit.
A single variable frequency drive (VFD) may control 2 or 3 motors at a time, multiple motors control is usually done because of budget considerations. When in this example below, a cooling tower with 4 equally sized motors are controlled by one variable frequency drive.
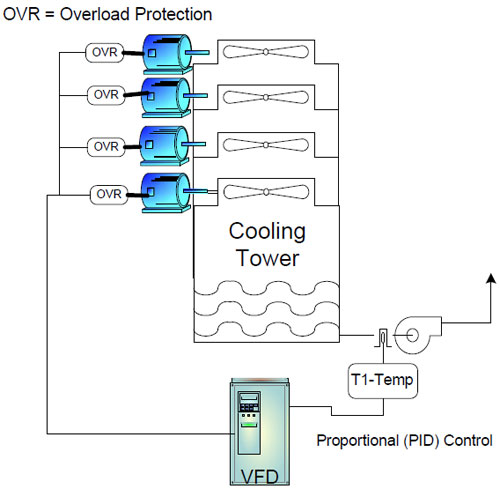
Please keep in mind that you can only set the VFD to V/F mode control if you control multiple motors by one variable frequency drive, never set variable frequency drive to any vector control, even at open loop with vector control, otherwise the variable frequency drive will fail.
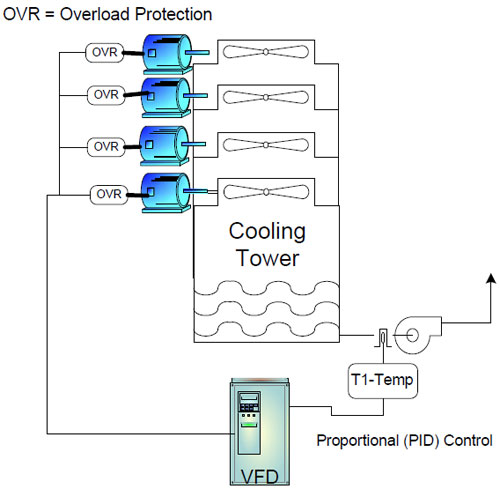
Please keep in mind that you can only set the VFD to V/F mode control if you control multiple motors by one variable frequency drive, never set variable frequency drive to any vector control, even at open loop with vector control, otherwise the variable frequency drive will fail.
Although dampers are commonly used to control the output of fans, reducing the speed of the fan by variable frequency drive (VFD) is a much more energy efficient method of achieving the same effect.
With damper control, the input power reduces as the flow rate decreases, however under variable frequency drive control the power reduction is far more dramatic. The variable torque characteristic of the fan means that the relationship between flow and the speed of the fan is such that the input power reduces in a cube law relationship with the speed reduction, as shown in the graph.
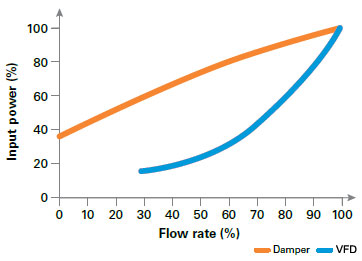
Note: When operating at near full speed there is a crossover point where variable frequency drive control can use more energy than fixed speed control with dampers. This is due to the losses in the variable frequency drive exceeding the savings from the speed reduction.
With damper control, the input power reduces as the flow rate decreases, however under variable frequency drive control the power reduction is far more dramatic. The variable torque characteristic of the fan means that the relationship between flow and the speed of the fan is such that the input power reduces in a cube law relationship with the speed reduction, as shown in the graph.
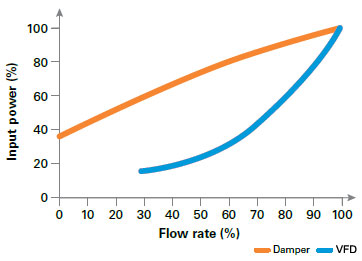
Note: When operating at near full speed there is a crossover point where variable frequency drive control can use more energy than fixed speed control with dampers. This is due to the losses in the variable frequency drive exceeding the savings from the speed reduction.
The purpose of this paper is to present possible solutions that can be used by mining companies for the mining and processing of stones for civil construction using Gozuk Variable Frequency Drives (VFD). Within this context this paper presents an approach of the mining processes, types of activities and possible gains with productivity, energy saving and reduction of mechanical breaks. From the conveyor belts of the mineral, crushers, size selecting screens for the crushed stones to even on the air filtering systems (bag filters), the variable frequency drives can be used with significant gains both in energy saving and in the increase of equipment production as well as in reducing mechanical breaks and stops for maintenance.
The mining process is very diversified and the composition of the ore/stones also varies even in the same mine which requires for the process to adapt to each case. It isn't always possible to achieve the wanted quality and ideal productivity with machines built considering an average composition or a specific case and without the use of variable frequency drives to set the speed.
The mining process is very diversified and the composition of the ore/stones also varies even in the same mine which requires for the process to adapt to each case. It isn't always possible to achieve the wanted quality and ideal productivity with machines built considering an average composition or a specific case and without the use of variable frequency drives to set the speed.
Quantifying the energy efficiency of pump units across markets is a tough task: These units mostly consist of rotodynamic pumps driven by motor systems either without or with variable frequency drives (VFD), the latter being called power drive systems (PDS). To evaluate the energy efficiency of such arbitrary pump units in the frame of the Extended Product Approach (EPA), the Energy-Efficiency-Index (EEI) is introduced as a normalized weighted average of electrical power input of a pump unit operated at different duty points of a standardized load-time profile. If the unit is equipped with a VFD, the duty points also have to be adjusted according to a standardized pressure control curve. The energy efficiency index is therefore a measure of energy efficiency and represents simultaneously the quality of the Extended Product "pump unit" and the characters of the standardized load-time profile and the standardized pressure control curve. The two general methodologies to determine the energy efficiency index presented in this article are valid independently of a particular standardized load-time profile or pressure control curve.
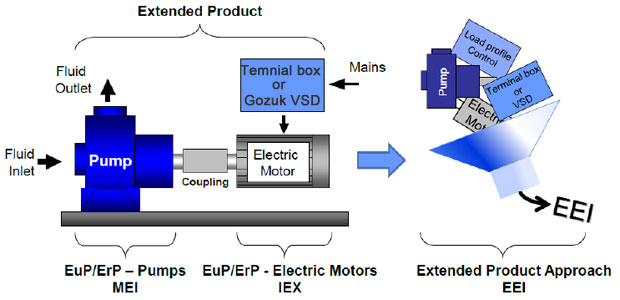
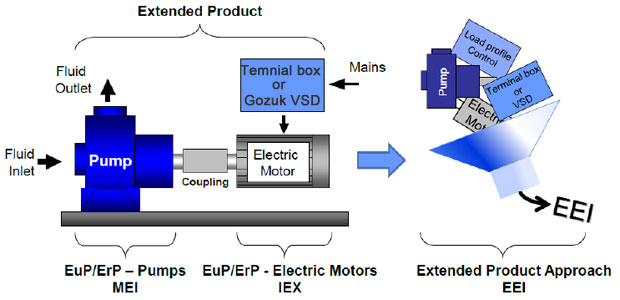
The bypass must switch the power supply to the motor between the variable frequency drive and the power line, but it also must be able to:
- Protect the motor in both variable frequency drive and bypass modes.
- Interface with safety controls.
- Isolate the variable frequency drive for service while maintaining motor operation.
- Meet code requirements as a motor starter.
Before selecting a Variable Frequency Drive (VFD) for an existing electric motor, it's important to know the purpose and characteristics of the different components involved in the process. This paper gives a list of the parameters that I looked at to make my selection about the needed VFD.
It's useful to choose a 4 quadrant variable frequency drive. This way DC-braking, AC-braking with resistor and/or maybe AC-braking with recovery can be done. Regenerative braking is also used in an electric vehicle so if an inert load is used this can be implemented in an experiment. The possibility of regenerative braking is not a major point to make the selection, more an interesting bonus.
It's useful to choose a 4 quadrant variable frequency drive. This way DC-braking, AC-braking with resistor and/or maybe AC-braking with recovery can be done. Regenerative braking is also used in an electric vehicle so if an inert load is used this can be implemented in an experiment. The possibility of regenerative braking is not a major point to make the selection, more an interesting bonus.
When installing a variable frequency drive is that the air ends (i.e. impellers) are usually custom made for the air compressor. For load/no load control systems, they are designed with a flight for running at 100%. Since you typically see energy savings with a VFD when the compressor runs in the 30 - 70% of max load, you may lose some efficiency with this as opposed to VFD air ends which are designed for 80% flow. You should be able to estimate this based on the literature.
I am of view that the variable frequency drive savings are rather application oriented. In constant torque applications like conveyors etc. the VFD savings as compared to DC drives are not great but savings are tremendously large compared to Eddy Current drives which now a days are rare to find. On the contrary, applications exhibiting centrifugal load characteristics yield tremendous savings depending upon normal running speed as a ratio to peak design speeds. Even one can expect to the tune of 65% to 70% depending upon empirical situations.
Variable Frequency Drive (VFD) technology is an essential component of state-of-the-art refrigeration and climate technology. When compared to conventional refrigeration technology, a few essential changes are required for safe, reliable plant operation. This paper describes in detail how a refrigeration system is dimensioned and how VFDs are installed in a refrigeration system.
In order to optimize a refrigeration system with an intelligent VFD, it is necessary to clearly understand the features of the electrical and control equipment and the possibilities afforded by using standard equipment. These excerpts describe the electrical design and also provide an example showing how a control system is connected-up in Figure 2.
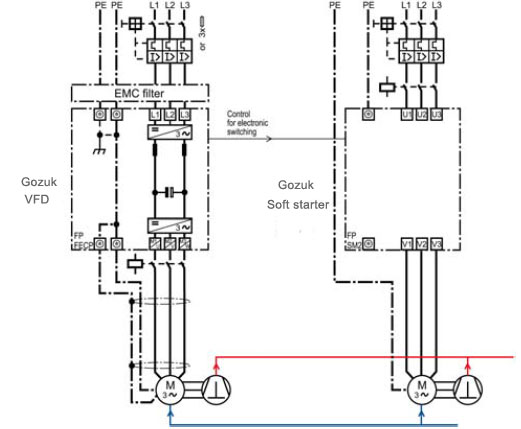
In order to optimize a refrigeration system with an intelligent VFD, it is necessary to clearly understand the features of the electrical and control equipment and the possibilities afforded by using standard equipment. These excerpts describe the electrical design and also provide an example showing how a control system is connected-up in Figure 2.
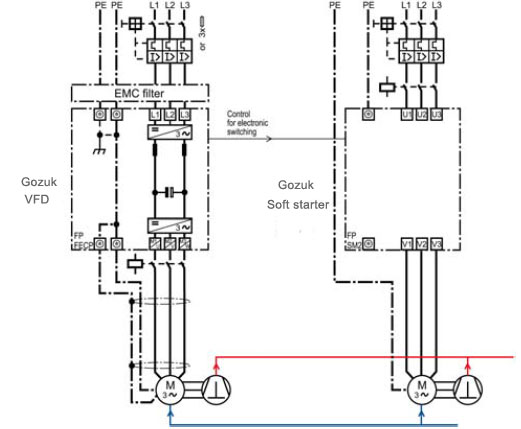
Featured Articles
Single VFD for Multiple Motors
A single variable frequency drive (VFD) may control 2 or 3 motors at a time, multiple motors control is usually done because of ...
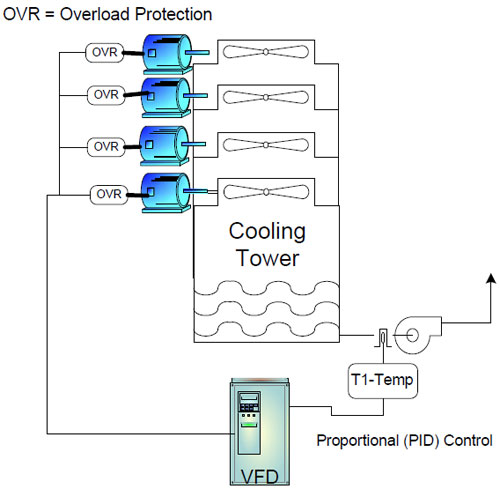
Variable frequency drive for water ...
Quantifying the energy efficiency of pump units across markets is a tough task: These units mostly consist of rotodynamic pumps ...
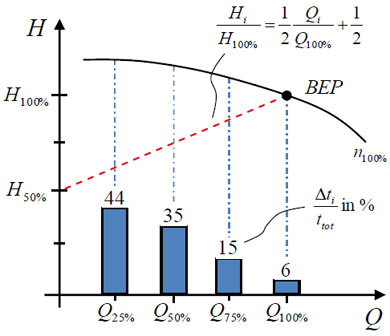
Select a right Variable Frequency Drive
Before selecting a Variable Frequency Drive (VFD) for an existing electric motor, it's important to know the purpose and ...
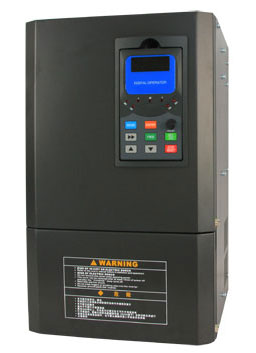
VFD on air compressor considerations
When installing a variable frequency drive is that the air ends (i.e. impellers) are usually custom made for the air compressor. ...
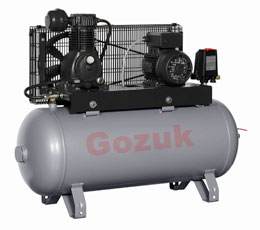
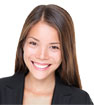
Variable Frequency Drives control AC motor for energy savings by adjustable speed, for short VFD, also named variable speed drives and frequency inverter.