Difference between MV and LV Variable Frequency Drives
The simple answer - that a medium voltage (MV) variable frequency drive (VFD) has a higher output voltage capability than a low voltage (LV) variable frequency drive (VFD) - is not the whole story.
A MV VFD will usually require a higher input voltage to achieve the higher output voltage, therefore connecting closer to the utility feeding the plant. This means larger / more expensive breakers and transformers on the upstream side - and larger, more expensive contactors inside the variable frequency drive cabinet.
A MV VFD is often physically larger than a comparable-power LV configuration. In part, this is because internal clearances have to be greater to prevent arcing faults. Also, the components related to the voltage level are typically larger in the MV VFD, requiring more room to mount.
MV VFDs are - almost exclusively - three phase connections both upstream and downstream from the variable frequency drive. Although a LV VFD can be similarly connected to three phase, there are a large percentage of LV VFDs that are single phase devices (either upstream, downstream, or both).
As usual, the "elephant in the room" is the losses related to power transmission. Essentially, as the current draw increases, so do the losses - requiring larger conductor cross-section and better thermal insulation. Going to a higher voltage allows the same power flow at reduced current (power is a product of voltage and current).
So - what we see is that MV VFDs are used for different (or at least larger) applications, simply due to the total electrical power requirement. As a sideline to this, the "brains" of the variable frequency drive are typically more complex in the larger MV VFDs as well, because they are being tasked with controlling more in the way of inputs - both from the concept of power flow to the load, and from a "process monitoring" aspect.
A MV VFD will usually require a higher input voltage to achieve the higher output voltage, therefore connecting closer to the utility feeding the plant. This means larger / more expensive breakers and transformers on the upstream side - and larger, more expensive contactors inside the variable frequency drive cabinet.
A MV VFD is often physically larger than a comparable-power LV configuration. In part, this is because internal clearances have to be greater to prevent arcing faults. Also, the components related to the voltage level are typically larger in the MV VFD, requiring more room to mount.
MV VFDs are - almost exclusively - three phase connections both upstream and downstream from the variable frequency drive. Although a LV VFD can be similarly connected to three phase, there are a large percentage of LV VFDs that are single phase devices (either upstream, downstream, or both).
As usual, the "elephant in the room" is the losses related to power transmission. Essentially, as the current draw increases, so do the losses - requiring larger conductor cross-section and better thermal insulation. Going to a higher voltage allows the same power flow at reduced current (power is a product of voltage and current).
So - what we see is that MV VFDs are used for different (or at least larger) applications, simply due to the total electrical power requirement. As a sideline to this, the "brains" of the variable frequency drive are typically more complex in the larger MV VFDs as well, because they are being tasked with controlling more in the way of inputs - both from the concept of power flow to the load, and from a "process monitoring" aspect.
Post a Comment:
You may also like:
Featured Articles
Variable Frequency Drive Sizing
Before selecting the size of a variable frequency drive (VFD), it is necessary to generally know the working environment, the ...
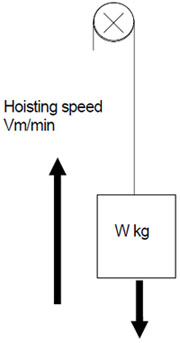
Single VFD for Multiple Motors
A single variable frequency drive (VFD) may control 2 or 3 motors at a time, multiple motors control is usually done because of ...
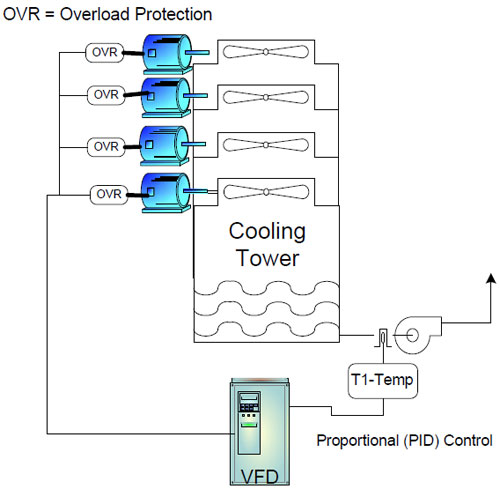
PWM Variable Frequency Drive ...
Pulse Width Modulation (PWM) voltage source variable frequency drives (VFD) presently comprehend the most used equipments to feed ...
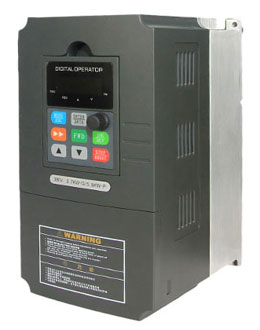
Variable frequency drive for water ...
Quantifying the energy efficiency of pump units across markets is a tough task: These units mostly consist of rotodynamic pumps ...
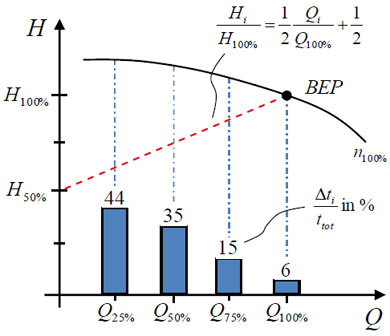
Variable Frequency Drive Basic Safety ...
This paper provides guidelines on functional safety considerations when selecting and integrating a variable frequency drive ...
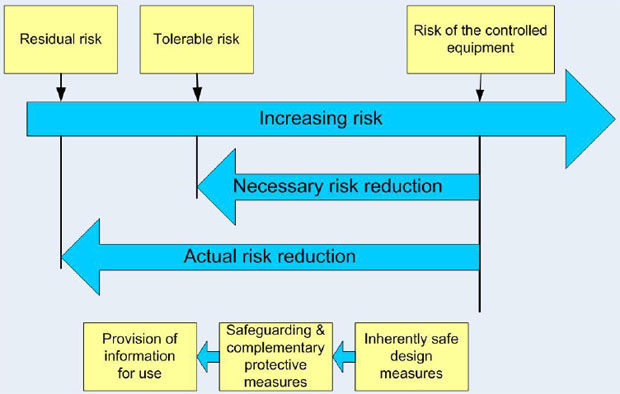
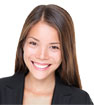
Variable Frequency Drives control AC motor for energy savings by adjustable speed, for short VFD, also named variable speed drives and frequency inverter.