Variable Frequency Drive
In short VFD, is an energy saving device by converting fixed frequency to adjustable frequency to control AC induction motor in variable speed base on the load's changes, also know as variable speed drive, frequency inverter and adjustable frequency drives. VFD also works as a phase converter to convert single phase input to three phase output in small ratings.As one of the professional manufacturers of low voltage variable frequency drives in China, we can supply a wide range VFD ratings, from 1/2 hp to 500 hp, with single phase 220V to three phase 380V.
Our variable frequency drives are widely used in China domestic companies, and have been export to India, Pakistan, Australia, South Africa, and much more countries. our VFD can be used in pumps, fans, injection molding machines, HVAC system, constant pressure water supply system and lots of other applications which need vary motor speed.
Latest Articles
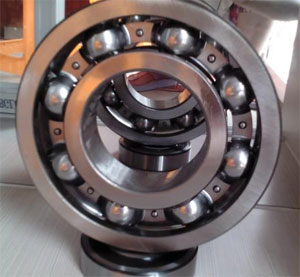
Compensatory externals to aid in starting torque generation for synchronous motors are also basically expense burdens that need not be borne.
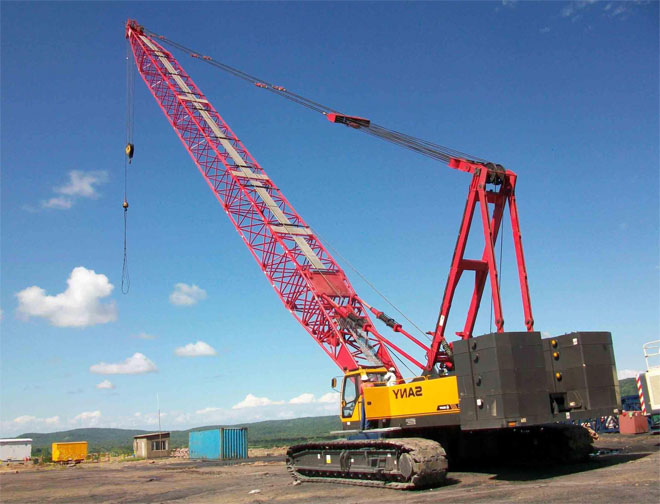
The cost of the synchronous motor itself over the asynchronous motor, with increased in frame size, added copper and other materials, is another base reason synch motors are seldom, if ever used in the overhead hoist and crane industry. As far as precise travel and lifting speeds with cranes, variable frequency drives with the hardware and software fairly standard on most variable frequency drives (VFD) designed for the application, is more than adequate. These variable frequency drives not only deliver excellent efficacy and significant energy savings by maintaining very good Volts/Hz/RPM ratios. Utilizing motor speed regulation at 0.5% without an encoder and 0.1% with asynchronous motors, makes the most opted for joint overhead crane control package.
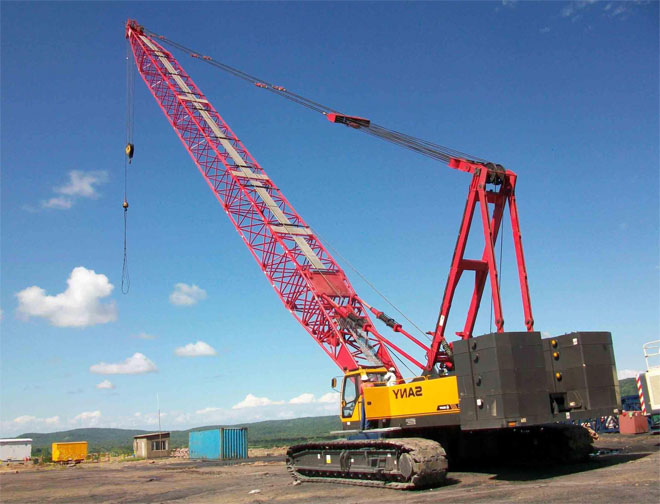
The cost of the synchronous motor itself over the asynchronous motor, with increased in frame size, added copper and other materials, is another base reason synch motors are seldom, if ever used in the overhead hoist and crane industry. As far as precise travel and lifting speeds with cranes, variable frequency drives with the hardware and software fairly standard on most variable frequency drives (VFD) designed for the application, is more than adequate. These variable frequency drives not only deliver excellent efficacy and significant energy savings by maintaining very good Volts/Hz/RPM ratios. Utilizing motor speed regulation at 0.5% without an encoder and 0.1% with asynchronous motors, makes the most opted for joint overhead crane control package.
A MV VFD is often physically larger than a comparable-power LV configuration. In part, this is because internal clearances have to be greater to prevent arcing faults. Also, the components related to the voltage level are typically larger in the MV VFD, requiring more room to mount.
MV VFDs are - almost exclusively - three phase connections both upstream and downstream from the variable frequency drive. Although a LV VFD can be similarly connected to three phase, there are a large percentage of LV VFDs that are single phase devices (either upstream, downstream, or both).
MV VFDs are - almost exclusively - three phase connections both upstream and downstream from the variable frequency drive. Although a LV VFD can be similarly connected to three phase, there are a large percentage of LV VFDs that are single phase devices (either upstream, downstream, or both).
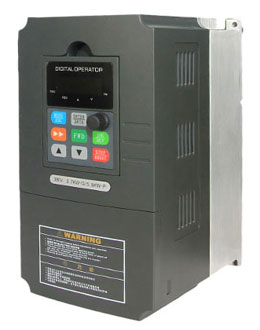
When using single stage pumps, the pump speed is critical, and the pump curve should be verified. But when using submersible pumps, these are typically multi-stage (maybe 15+ stages) and can be reduced much lower in speed. With centrifugal pumps, of course efficiency drops off. Fans have a much lower threshold as where they become ineffective. We have done many pump and fan variable drive applications in the last 30 years, and turning the speed down has never been a problem... With constant-torque applications, it is not recommended to go below 30% even when using a severe duty motor.
V/F control
This is a control system in which the ratio of frequency to the output voltage is constant when the frequency is changed. In this system, if the voltage to be actually valid decreases due to a voltage drop in a wiring or the primary coil of a motor, enough amount of torque cannot be output (the slower the speed is, the more this phenomenon affects.). Therefore, the amount of voltage drop estimated in advance is set higher (torque boost) to cover the shortage of the torque at low speed.
Vector control
Detect a motor speed with an encoder and calculate a motor slip to identify the load magnitude. This control is a system which divides the variable frequency drive output current into an excitation current (a current necessary to generate a magnetic flux) and a torque current (a current proportional to the load torque) by vector calculation and controls a frequency and voltage optimally to flow a necessary current individually according to this load magnitude.
This is a control system in which the ratio of frequency to the output voltage is constant when the frequency is changed. In this system, if the voltage to be actually valid decreases due to a voltage drop in a wiring or the primary coil of a motor, enough amount of torque cannot be output (the slower the speed is, the more this phenomenon affects.). Therefore, the amount of voltage drop estimated in advance is set higher (torque boost) to cover the shortage of the torque at low speed.
Vector control
Detect a motor speed with an encoder and calculate a motor slip to identify the load magnitude. This control is a system which divides the variable frequency drive output current into an excitation current (a current necessary to generate a magnetic flux) and a torque current (a current proportional to the load torque) by vector calculation and controls a frequency and voltage optimally to flow a necessary current individually according to this load magnitude.
General-purpose motors and vector variable frequency drive (VFD) dedicated motors are three-phase induction motors. These motors mainly consist of a rotary shaft, bearings, stator winding and connection terminals. Vector VFD dedicated motors have an encoder at the rear of their rotary shaft. These components must be inspected periodically to prevent any fault from occurring due to the adverse effects from the operating environment, such as temperature, humidity, dust, dirt and vibration, changes in the parts with time, service life, and other factors.
A variable frequency drive (VFD) is a static unit mainly consisting of semiconductor devices. Daily inspection must be performed to prevent any fault from occurring due to the adverse effects from the operating environment, such as temperature, humidity, dust, dirt and vibration, changes in the parts with time, service life, and other factors.
A variable frequency drive (VFD) is a static unit mainly consisting of semiconductor devices. Daily inspection must be performed to prevent any fault from occurring due to the adverse effects from the operating environment, such as temperature, humidity, dust, dirt and vibration, changes in the parts with time, service life, and other factors.
1) The leakage breaker or leakage relay may operate unintentionally due to the leakage current between grounds. The leakage current includes many high frequency components that have a relatively small influence on human body.
2) The external thermal relay may operate unintentionally due to the leakage current between cables.
2) The external thermal relay may operate unintentionally due to the leakage current between cables.
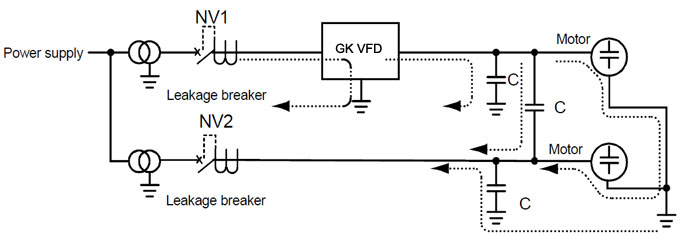
Variable frequency drives convert incoming alternating current (AC) to direct current (DC) and then invert the DC power into variable frequencies and voltage AC power. Most variable frequency drives produce a constant voltage/frequency (hz)ratio.
One of the most common methods of varying pump shaft speed is to use a VFD. These VFDs take advantage of the fact that torque, speed and horsepower of an AC electric motor are related to the frequency and voltage of the electrical power supply.
For the VFD to be a sensible solution to your pumping application the system curve would have to fall on, or close to this best efficiency point line, or you will experience radial loads that will translate to shaft deflection. Most centrifugal pump companies want you to operate within 5% to 10% of the best efficiency point. Heavy duty pumps that have a low L3/D4 (shaft diameter to shaft length ratio) have a much larger operating window.
One of the most common methods of varying pump shaft speed is to use a VFD. These VFDs take advantage of the fact that torque, speed and horsepower of an AC electric motor are related to the frequency and voltage of the electrical power supply.
For the VFD to be a sensible solution to your pumping application the system curve would have to fall on, or close to this best efficiency point line, or you will experience radial loads that will translate to shaft deflection. Most centrifugal pump companies want you to operate within 5% to 10% of the best efficiency point. Heavy duty pumps that have a low L3/D4 (shaft diameter to shaft length ratio) have a much larger operating window.
Among the most successful strategies managers have at their disposal for controlling electrical energy use and minimizing utility costs is the use of variable frequency drive (VFD). Incorporating variable frequency drives into applications such as fans, pumps, and cooling towers can reduce energy use up to 50 percent at partial loads by matching motor speed to the changing load and system requirements.
They also feature better operator interface features, including:
They also feature better operator interface features, including:
- start, stop and speed adjustment
- reversing and toggling between manual and automatic speed adjustment from an external process control signal
- alpha-numeric display, indicator lights, and meters to provide text information for communication and maintenance
- a front-mounted or cable-connected keypad for input
- input/output terminals available for push buttons, switches and other interface devices
- serial communication port for variable frequency drive configuring, monitoring and controlling using a computer
- loading of parameter settings from one VFD to another
- multi-day timers
- broadcast function to control dozens of VFDs from one advanced operator panel.
The energy saving of variable frequency drives (VFD) in industrial applications is well understood by engineers, but awareness is less widespread at cheque signing level - amongst financial teams, senior management and purchasing departments. The systems thinking and good communication is the key to tackling this problem and improving everybody's bottom line.
China industry and commerce can save 30% of its energy costs, which represents a significant 3% addition to the bottom line. All it has to do is implement a single, simple energy saving measure - fitting VFDs to its electric motors. However, I'm quite conscious that there are plenty of technologies out there claiming to be the panacea of all environmental ills. But in the case of the variable frequency drive, there is a real, mathematically demonstrable, argument.
China industry and commerce can save 30% of its energy costs, which represents a significant 3% addition to the bottom line. All it has to do is implement a single, simple energy saving measure - fitting VFDs to its electric motors. However, I'm quite conscious that there are plenty of technologies out there claiming to be the panacea of all environmental ills. But in the case of the variable frequency drive, there is a real, mathematically demonstrable, argument.
Applying a variable frequency drive (VFD) to the heating system (see Figure 2) and a temperature sensor, the hot water temperature to the building zones can be better maintained by varying the flow of water.
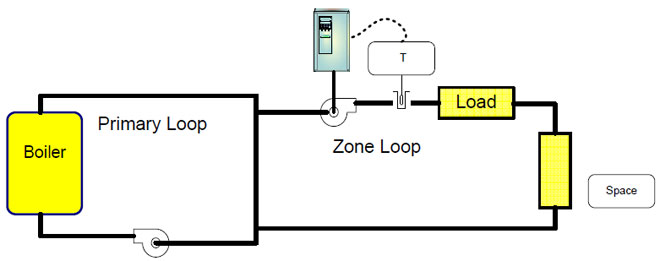
Energy Savings result from reduced electrical costs by reducing the speed of the pump and by better temperature control - preventing temperature over-shoot (over heating) in the zones. In many applications the pumps are oversized (10 to 15%), so even in maximum heat load conditions, the maximum pump speed with the variable frequency drive is less than before the retrofit.
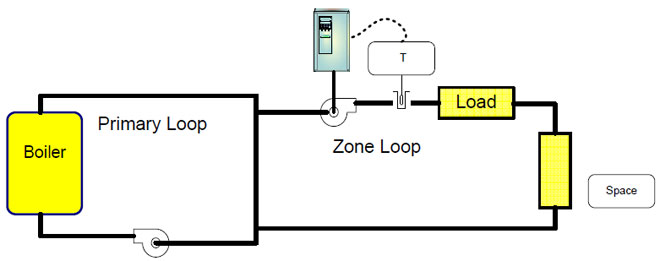
Energy Savings result from reduced electrical costs by reducing the speed of the pump and by better temperature control - preventing temperature over-shoot (over heating) in the zones. In many applications the pumps are oversized (10 to 15%), so even in maximum heat load conditions, the maximum pump speed with the variable frequency drive is less than before the retrofit.
A soft starter reduces voltage, not Hertz, and as such the starting torque at 2-3 Hz is next to nothing. The soft starter is essentially robbing the motor of voltage at all points between 0 and 59 Hz, peak (Line) voltage met at 60 Hz. In overhead crane controls, setting a soft start to begin traversal motions with a capacity load on the crane or trolley can result in a 'jack rabbit' starting jump when the crane is unloaded. Or, setting it when unloaded can result in motor thermal trip and no motion achieved when the crane is then capacity loaded.
When compare with a variable frequency drive (VFD), the motor peak design ratio is basically preserved throughout the acceleration ramp. To put this in a general, simple explanation, when a 460 VAC/60 Hz motor is running at 30 Hz, the corresponding voltage to the motor should be in the vicinity of 230 VAC. Changing one value in the Volts to Hertz ratio without changing the other results in significant motor torque loss. A VFD will provide smooth starts from zero to peak speed as with the Hz/Voltage ratio maintained, near peak motor torque is preserved. Unlike a soft starter, it will provide the same balance ratio and control effect in a deceleration ramp as well.
When compare with a variable frequency drive (VFD), the motor peak design ratio is basically preserved throughout the acceleration ramp. To put this in a general, simple explanation, when a 460 VAC/60 Hz motor is running at 30 Hz, the corresponding voltage to the motor should be in the vicinity of 230 VAC. Changing one value in the Volts to Hertz ratio without changing the other results in significant motor torque loss. A VFD will provide smooth starts from zero to peak speed as with the Hz/Voltage ratio maintained, near peak motor torque is preserved. Unlike a soft starter, it will provide the same balance ratio and control effect in a deceleration ramp as well.
Featured Articles
Variable Frequency Drive Sizing
Before selecting the size of a variable frequency drive (VFD), it is necessary to generally know the working environment, the ...
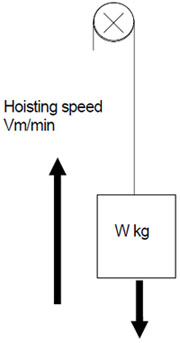
Single VFD for Multiple Motors
A single variable frequency drive (VFD) may control 2 or 3 motors at a time, multiple motors control is usually done because of ...
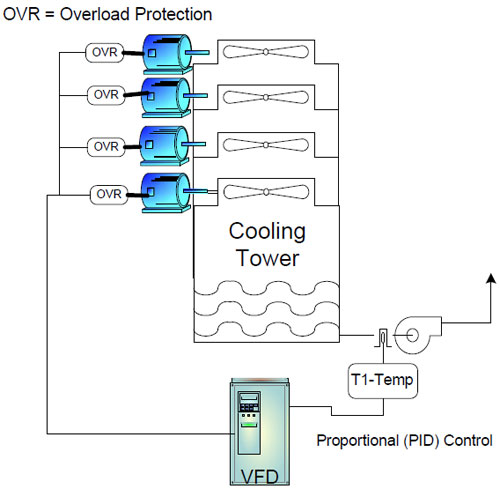
PWM Variable Frequency Drive ...
Pulse Width Modulation (PWM) voltage source variable frequency drives (VFD) presently comprehend the most used equipments to feed ...
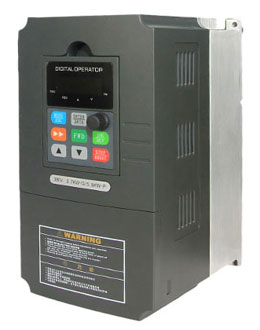
Variable frequency drive for water ...
Quantifying the energy efficiency of pump units across markets is a tough task: These units mostly consist of rotodynamic pumps ...
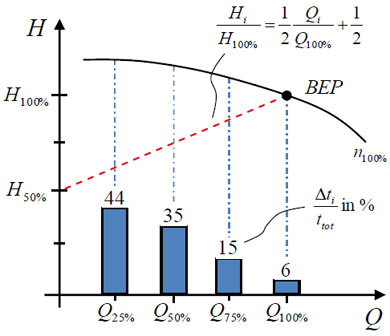
Variable Frequency Drive Basic Safety ...
This paper provides guidelines on functional safety considerations when selecting and integrating a variable frequency drive ...
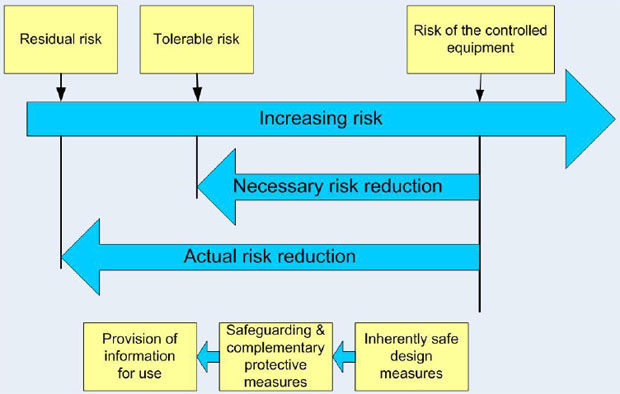
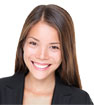
Variable Frequency Drives control AC motor for energy savings by adjustable speed, for short VFD, also named variable speed drives and frequency inverter.